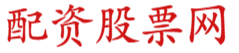

136-8172-4809(V同号)目前PA12价格处于低位,我司有各种品牌、型号、规格的PA12材料出售,原厂原包,物美价廉,欢迎选购!
PA12(聚酰胺12)是尼龙家族中性能独特的成员,具有熔点低、吸水率低(仅0.2-0.5%)、耐低温性优异(-40℃仍保持韧性)、耐化学性好等特点,广泛用于汽车管路、医疗器械、运动器材等领域。其注塑成型工艺需结合材料特性针对性控制,以下从全流程详细说明:
一、原料准备:干燥处理
PA12虽吸水率低,但注塑前仍需严格干燥(微量水分会导致熔体降解,产生气泡、银丝等缺陷)。
- 干燥条件:温度80-100℃,时间4-6小时,露点≤-40℃(建议用热风循环干燥机或除湿干燥机)。
- 判断标准:干燥后原料含水率需≤0.05%,可通过称重法(干燥前后重量差)或注塑试模(无气泡、银丝)验证。
展开剩余80%二、注塑机选型
- 螺杆类型:优先选用渐变型螺杆(压缩比2.5-3.5),避免剪切过强导致材料降解;长径比(L/D)20-25(确保塑化均匀)。
- 料筒材质:普通制品用氮化钢螺杆;增强型PA12(如加玻纤)需用双金属螺杆(防磨损)。
- 锁模力:根据制品投影面积计算,一般500-800kN/m²(比PA6/PA66低10-20%,因熔体流动性更好)。
三、核心工艺参数控制
1. 温度参数(关键!影响熔体流动性和稳定性)
PA12熔点170-180℃,分解温度>300℃,工艺温度需介于熔点与分解温度之间:
- 料筒温度(分段控制,避免局部过热):
- 后段(进料段):190-210℃(预热原料,防止螺杆打滑);
- 中段(塑化段):200-220℃(主要塑化区,确保完全熔融);
- 前段(计量段):180-200℃(稳定熔体温度,避免过度降解)。
- 喷嘴温度:180-200℃(略低于前段,防止流涎;堵塞时可短暂升至210℃清理)。
- 注意:温度过高(>240℃)会导致材料黄变、力学性能下降(冲击强度降低30%以上)。
2. 模具温度
直接影响制品结晶度、表面质量和内应力:
- 常规制品:40-60℃(平衡外观与生产效率,表面光泽度适中);
- 高韧性/尺寸稳定制品:60-80℃(提高结晶度,降低内应力,冲击强度提升10-15%);
- 薄壁复杂件:50-70℃(避免冷却过快导致填充不足)。
- 控温方式:建议用油温机(温度波动≤±2℃),比水温机更适合高温需求。
3. 注射与保压参数
- 注射压力:60-100MPa(PA12熔体粘度低,压力无需过高);
- 薄壁件(<1mm)或复杂结构:80-100MPa(确保型腔充满);
- 厚壁件(>3mm):60-80MPa(防止飞边)。
- 注射速度:10-50mm/s(中等速度为宜);
- 表面要求高的制品:20-30mm/s(避免熔体破裂);
- 需消除熔接痕:30-50mm/s(提高熔体融合性)。
- 保压压力:注射压力的50-70%(60-70MPa),时间5-20s(根据厚度:1mm厚度≈2-3s),防止缩痕。
4. 冷却时间
取决于制品厚度和模温:
- 厚度1-3mm:10-15s;
- 厚度3-5mm:15-25s;
- 原则:确保制品脱模时温度≤60℃(避免变形)。
四、常见缺陷及解决方法
缺陷 | 典型原因 | 解决措施 |
------------|---------------------------|-------------------------------------------|
银丝/气泡 | 干燥不足或料温过高 | 提高干燥温度至90℃,延长时间;降低料筒温度10-20℃ |
缩痕 | 保压不足或模温过低 | 提高保压压力10-20%;模温升高10-20℃ |
飞边 | 注射压力过高或锁模力不足 | 降低注射压力;检查锁模力(需≥注射压力×投影面积) |
熔接痕 | 熔体融合性差 | 提高料温/模温10-20℃;增加注射速度10-20mm/s |
开裂 | 内应力过大 | 模温提高至60-80℃;增加退火处理(80℃×1h) |
五、后处理:消除内应力
PA12制品因冷却速度不均可能残留内应力,导致存放或使用中开裂:
- 退火处理:将制品放入烘箱,80-100℃保温1-2小时,随炉缓慢冷却至室温(降温速率≤5℃/min)。
六、特殊类型PA12的工艺调整
- 玻纤增强PA12(如30%玻纤):
- 料筒温度提高10-20℃(200-230℃),确保玻纤与基体融合;
- 螺杆转速降低10-15%(减少玻纤断裂)。
- 增韧PA12:
- 模温控制在50-70℃(避免增韧剂析出);
- 保压时间缩短5-10%(减少内应力)。
通过严格控制干燥、温度、压力等参数工行炒汇杠杆,PA12可稳定成型出表面光洁、尺寸精准、性能优异的制品。
发布于:上海市Powered by 股票配资门户_在线炒股配资_最专业股票配资平台 @2013-2022 RSS地图 HTML地图